Your garage floor takes a beating. Between vehicles, weather, and storage woes, it’s crucial to choose a durable and cost-effective solution. Enter the concrete garage floor, a classic choice lauded for its strength and longevity. But before you break ground (or, well, pour concrete), you need a clear estimate of the financial impact. That’s where a concrete garage floor cost calculator comes in handy.
This article dives into the world of concrete garage floor costs, equipping you with a calculator tool and guiding you through the factors that influence the final price tag.
After calculating your concrete garage floor costs, maintain your investment with the best garage concrete floor cleaners, ensuring longevity and cleanliness.
Unveiling the Mystery: Calculating Your Concrete Garage Floor Cost
You can unlock the project’s cost secrets with careful calculations and informed considerations:
Step 1: Measure and Define
- Dimensions: Grab your tape measure and accurately record your garage’s length, width, and desired concrete thickness. Remember, thicker slabs come with a heavier price tag.
- Mix Strength: Choose your concrete mix based on intended use and durability needs. Higher strength translates to higher cost. Research common options like standard, high-strength, or fiber-reinforced mixes.
- Location: Enter your zip code to account for regional variations in material and labor costs. Local pricing can significantly impact your final estimate.
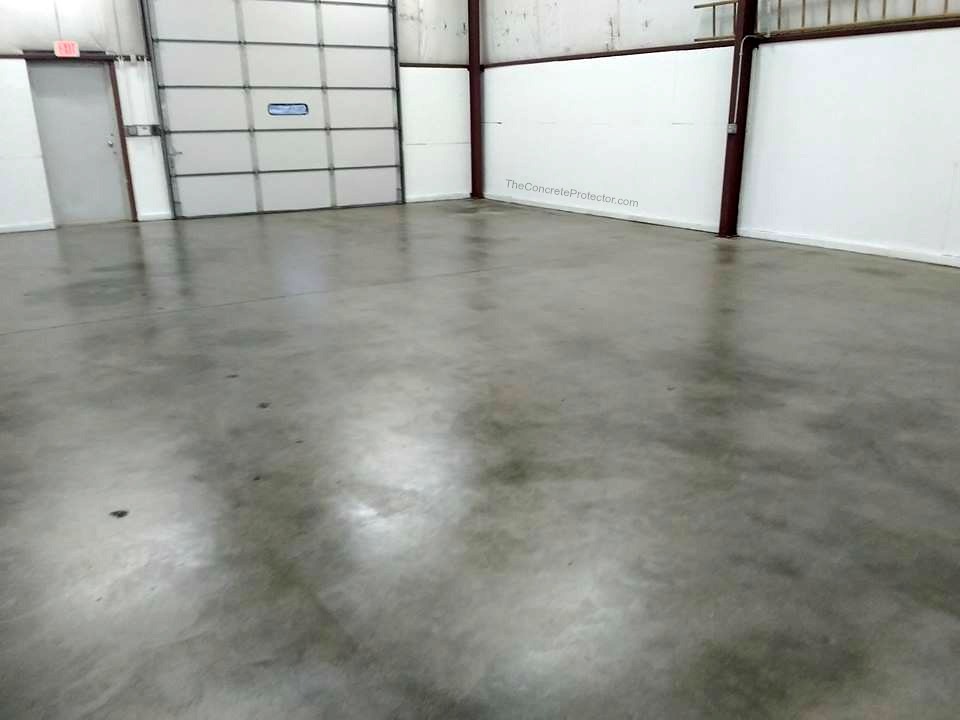
You may also like: 7 Best Black Garage Floor Paint Reviews
Step 2: Beyond the Basics
Think beyond the bare foundation. Consider these potential add-ons:
- Jointing: Prevents unsightly cracks, but adds to the cost. Research joint spacing and pattern options.
- Sealing: Creates a polished, protected surface, but requires additional materials and labor. Explore various sealant types and their price differences.
- Reinforcement: Essential for heavy loads or expansive areas, but significantly increases overall cost. Consult professionals for specific reinforcement needs.
- Existing Floor Removal: If your garage already has a floor, removing it adds another cost layer. Factor in disposal fees and labor associated with demolition.
Step 3: Unveiling the Estimate
Once you’ve gathered all the information, it’s time to put pen to paper (or fingers to calculator!):
- Material Cost: Research the average cost per cubic yard of your chosen concrete mix in your area. Multiply that price by your calculated concrete volume (length x width x thickness) to estimate material costs.
- Labor Cost: Contact local contractors or concrete suppliers for average labor rates per square foot of installation. Multiply this rate by your garage’s floor area to estimate labor costs.
- Add-On Costs: Research and add the individual costs of your chosen add-ons (jointing, sealing, reinforcement, removal) to the base cost.
But remember, these calculations provide an estimate, not a definitive price. Unexpected factors like site access, soil conditions, and contractor availability can influence the final cost.

By understanding the key calculations and considerations, you’ll be well-equipped to estimate your concrete garage floor cost and approach your project with informed confidence.
Beyond the Calculator: Key Factors Affecting Your Concrete Garage Floor Cost
The cost calculator paints a simplified picture, but a true understanding requires delving deeper into the factors influencing your final bill. Consider these key elements.
Concrete Mix: A Balancing Act of Strength and Cost
- Standard Mix: The budget-friendly option, suitable for standard garages with moderate loads. Think of it as the sturdy foundation of a budget-conscious build.
- High-Strength Mix: When heavy vehicles or extreme climates are in the equation, this mix is your knight in shining armor. Be prepared for a heftier price tag, however, as enhanced strength comes at a premium.
- Specialty Mixes: Craving heated floors or a polished finish? Specialized mixes cater to these desires, but expect them to add a significant chunk to your budget.
Thickness: Durability Comes with a Price
- Thin Slabs (4-5 inches): Perfect for pedestrian traffic and light storage, but might crack under heavier loads. Cost-effective, but consider future needs before going too thin.
- Standard Slabs (6-8 inches): The “Goldilocks Zone” for most garages, offering a good balance of durability and affordability.
- Heavy-Duty Slabs (10+ inches): The ultimate fortress for extreme loads or commercial use. Be prepared for a significant cost increase due to the additional material and labor required.
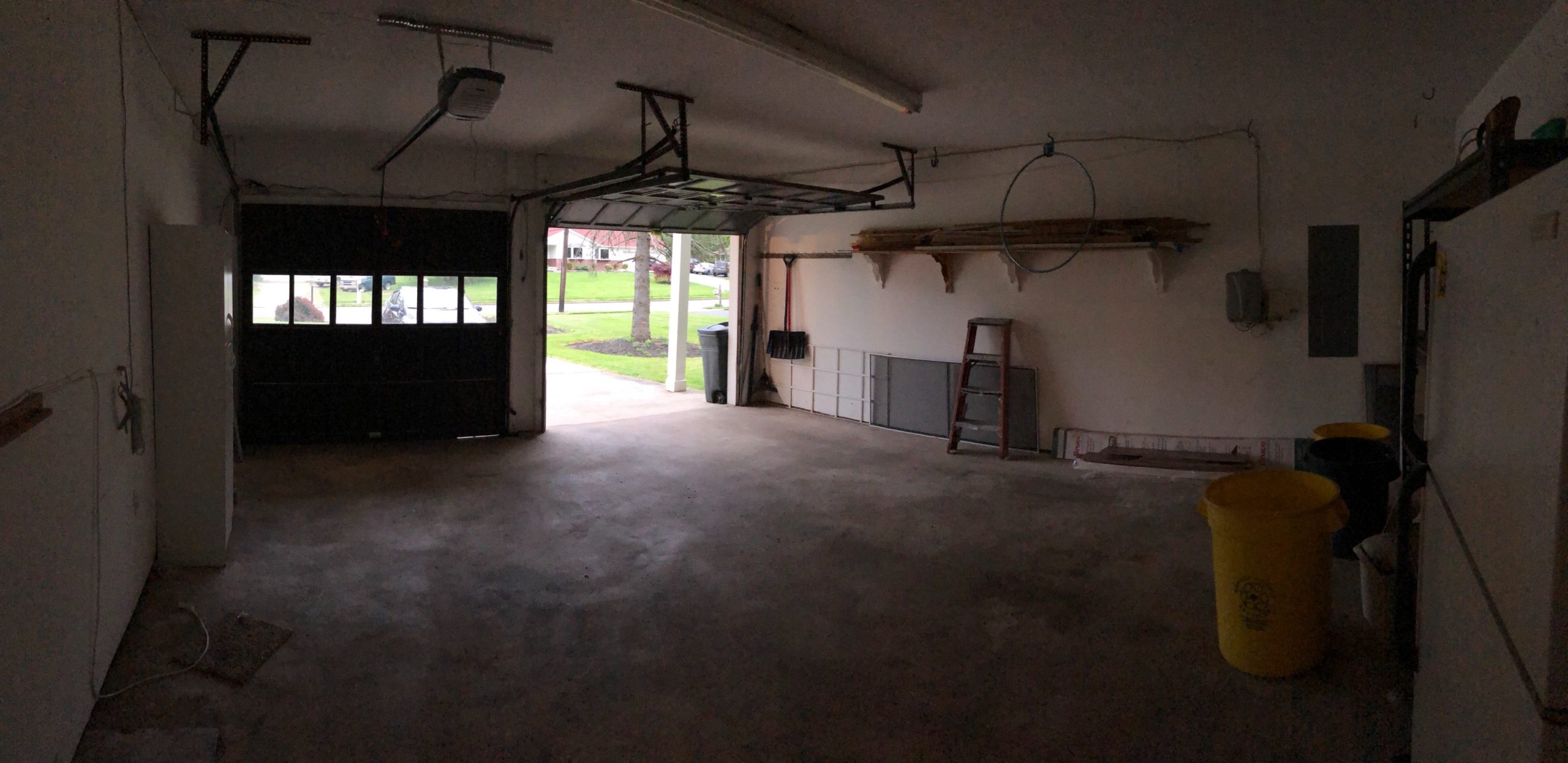
Subgrade Preparation: The Unsung Hero (or Villain)
- Level and Stable Base: Ideal scenario, requiring minimal preparation and keeping costs down. Think of it as building on a solid foundation.
- Uneven Surfaces: This is where things get interesting. Excavation, leveling, and additional materials might be necessary, adding to the initial estimate.
Accessibility: Geography Matters
- Easy Access: Concrete trucks can maneuver easily, minimizing delivery charges and keeping costs predictable.
- Remote Location or Tight Driveways: Expect additional fees for longer delivery distances or specialized equipment needed to reach your garage.
Labor Costs: The Expertise Factor
- Local Rates: Hourly wages for experienced concrete finishers vary greatly by location. Research your area’s average to get a realistic picture.
- Project Complexity: Simple pours cost less than intricate designs with specialized finishes. Remember, skilled labor comes at a premium.
Permits and Inspections: Navigating the Regulatory Maze
- Local Regulations: Some regions require permits and inspections, adding fees to your final bill. Factor these potential costs into your budget.
- Proactive Approach: Obtaining permits early streamlines the process and avoids potential delays or fines.

Additional Features: The Final Touches
- Jointing: Prevents unsightly cracks but adds to the labor cost.
- Sealing: Enhances aesthetics and protects the concrete, but comes with an additional price tag.
- Reinforcement: Crucial for heavy loads or specific designs, but be prepared for increased costs.
- Decorative Finishes: From polished concrete to epoxy coatings, these add visual appeal but also add to the overall expense.
The calculator provides a starting point, but these factors paint a more nuanced picture of your project’s true cost. By understanding these elements, you can make informed decisions, avoid hidden surprises, and confidently navigate the path to your dream concrete garage floor.
You may also like: 7 Best Garage Floor Containment Mats for Winter
Pro Tips for Using the Calculator and Saving Money
The concrete garage floor cost calculator is your first step, but true mastery comes with these pro tips.
Beyond the Algorithm: Seek Multiple Estimates
The calculator is a valuable tool, but it’s not a fortune teller. Don’t rely solely on its predictions. Contact local concrete contractors for customized estimates that factor in your specific needs, site conditions, and their unique pricing structures. This helps ensure you get the best value and avoid unpleasant surprises.
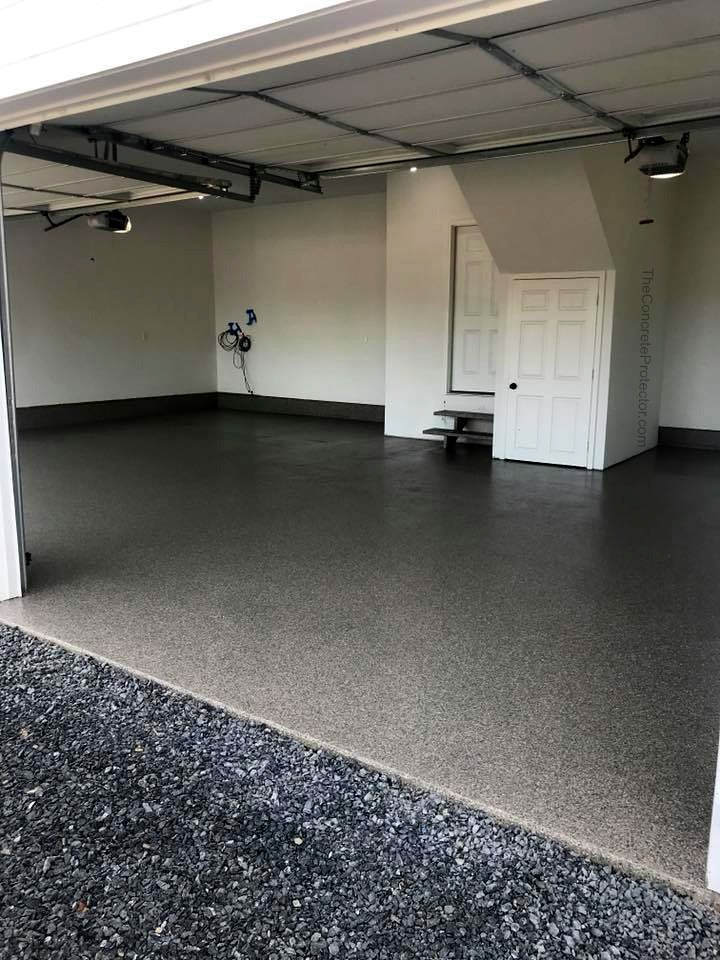
Unleash Your Inner DIY Hero (But Tread Carefully)
Are you handy with tools and possess a healthy dose of confidence? Consider tackling smaller projects yourself to save on labor costs. Think basic prep work, like removing existing flooring or basic jointing. However, proceed with caution. Factor in equipment rental fees, potential material waste due to inexperience, and the cost of fixing any mistakes.
Become a Material Maven: Explore Alternatives
Not all concrete mixes are created equal. While standard mixes are budget-friendly, explore alternative options like recycled materials or locally sourced aggregates that might offer cost savings without compromising quality. Research their suitability for your project and discuss them with contractors to find the best balance between affordability and performance.
Future-Proof Your Floor: Think Ahead, Save Later
Planning for the future can save you money in the long run. If you envision installing car lifts, workshops, or heavy equipment in your garage, consider incorporating thicker slabs or reinforcements during the initial pour. This might seem like an upfront cost, but it’s significantly cheaper than modifying an existing floor later.
Befriend the Permitting Process: Avoid Costly Delays
Don’t wait until the last minute to deal with permits and inspections. Research local regulations early and factor any associated fees into your budget. Proactive planning ensures a smooth process and avoids potential delays or fines that can derail your project and inflate costs.
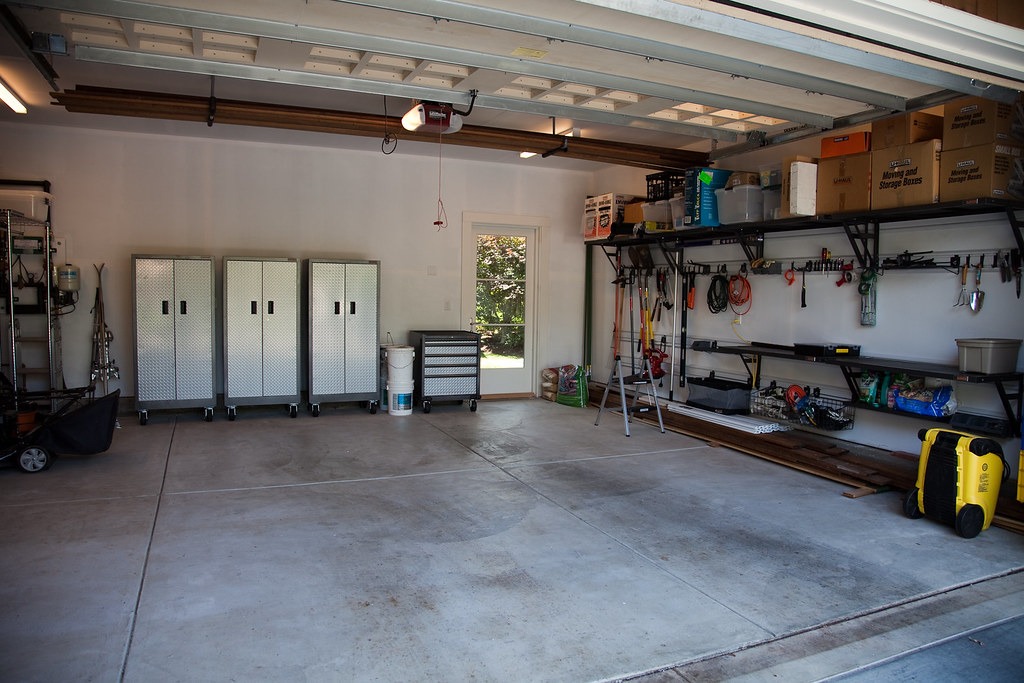
Negotiate Like a Pro: Knowledge is Power
Once you have multiple estimates and a thorough understanding of your project’s requirements, don’t be afraid to negotiate. Discuss your budget openly with contractors and see if they can offer flexibility or alternative solutions. Remember, a friendly and informed approach can often lead to mutually beneficial agreements.
Embrace the DIY Spirit (Smartly)
While tackling major tasks yourself might not be advisable, consider smaller DIY projects that add personal touches and save on costs. Think painting the walls, installing shelves, or adding basic lighting. Remember, even small DIY additions can contribute to a customized and functional garage space.
By understanding the influencing factors and considering alternatives, you can make informed decisions and ensure your new garage floor is both budget-friendly and built to last.
You may also like: 7 Best Apartment Garage Kits
Demystifying the Garage Concrete Slab Cost: From Square Feet to Budget Bliss
The dream of a gleaming, sturdy concrete slab adorning your garage floor is enticing, but the question “how much does it cost?” can quickly turn dreams into cold sweats.
While a definitive answer hinges on various factors, this guide sheds light on the intricate dance between square footage, materials, and hidden costs, empowering you to estimate your project with confidence.
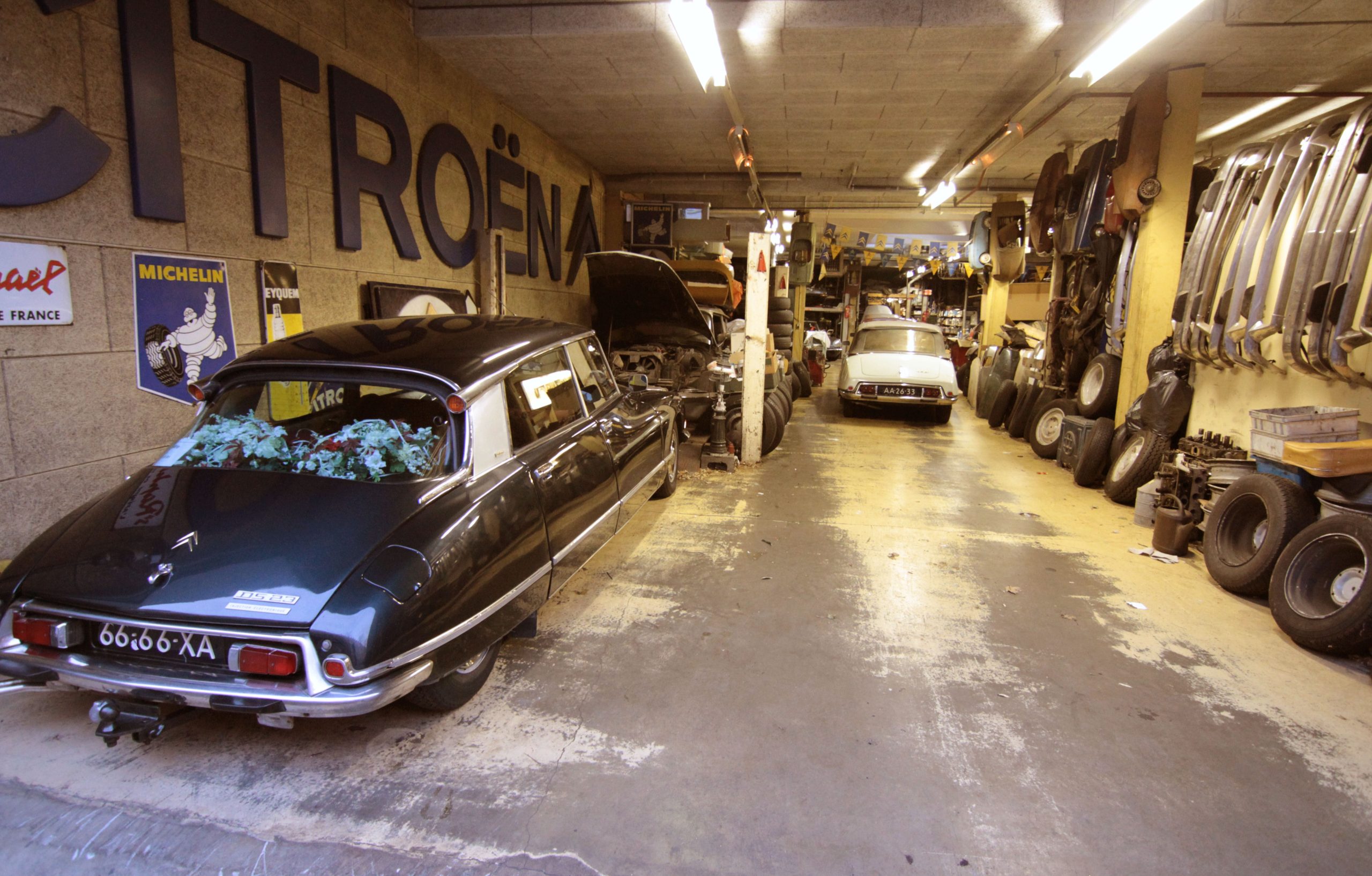
The Square Footage Shuffle: A Base for Budgeting
Imagine your garage floor as a blank canvas, its size dictating the amount of concrete needed, and consequently, a significant portion of the cost. Here’s the breakdown:
- Small Slabs (100-200 sq. ft.): Perfect for single-car garages or storage areas. Expect costs to range from $2,000 to $4,000.
- Standard Slabs (200-400 sq. ft.): Ideal for most two-car garages. Budget between $4,000 and $7,000.
- Large Slabs (400+ sq. ft.): Accommodate oversized vehicles or workshops. Anticipate costs exceeding $7,000.
Remember, this is just a starting point. Consider factors like thickness and desired strength for a more accurate estimate.
Concrete Garage Floor Maintenance & Cleaning: Cost-Cutting Tips
While concrete is a durable and cost-effective choice for your garage floor, it’s not maintenance-free. Understanding the ongoing costs of upkeep and implementing smart cleaning strategies can help you significantly reduce spending over time.

Understanding Maintenance Costs:
- Crack repair: Cracks can occur due to temperature changes, weight stress, or poor installation. Ignoring them leads to water infiltration, spalling, and costly repairs. Expect to pay $3-10 per linear foot for professional crack repair.
- Sealing: Concrete is porous and absorbs liquids, leading to stains and potential damage. Regular sealing (every 1-2 years) prevents this, costing $0.25-0.50 per square foot.
- Cleaning: Frequent cleaning removes dirt, grime, and spills, preventing stains and protecting the sealant. Simple cleaning supplies like degreasers and mops are relatively inexpensive, but professional cleaning services can cost $100-200 per session.
- Rejuvenation: Over time, concrete loses its shine and develops wear. Refinishing or polishing adds a protective layer and enhances aesthetics, but can cost $2-5 per square foot.
You may also like: 8 Best Garage Floor Drain Systems to Buy
Cost-Cutting Strategies:
- Preventative maintenance: Address cracks promptly, applying a high-quality sealant initially and resealing regularly. This significantly reduces the need for costly repairs and refinishing.
- DIY cleaning: Opt for DIY cleaning with affordable degreasers and mops. Consider a pressure washer for deep cleaning, but choose a low-pressure setting to avoid damaging the concrete.
- Natural cleaning solutions: Explore eco-friendly alternatives like vinegar and baking soda for regular cleaning. They’re often cheaper and gentler on the environment.
- Minimize spills: Promptly clean up spills, especially oil and chemicals, to prevent staining and potential damage. Use drip pans under vehicles and consider oil-absorbing mats.
- Proper drainage: Ensure proper drainage to prevent water pooling and potential damage to the concrete. Consider sloping the floor slightly towards a drain or installing a drainage channel.
- Invest in quality: While initially more expensive, high-quality sealants and cleaning products typically last longer and offer better protection, reducing long-term costs.
Bonus Tip: Utilize natural ventilation whenever possible to reduce moisture buildup and the growth of mold, which can require professional cleaning and remediation.
By implementing these strategies, you can significantly reduce the cost of maintaining and cleaning your concrete garage floor, ensuring it remains durable, aesthetically pleasing, and cost-effective for years to come.